Lean Transformation of Customer Service Operations
As the Lean Project Manager, I led a performance improvement initiative within a customer service operation, focusing on eliminating waste, optimizing processes, and enhancing customer satisfaction. This project required a data-driven approach and a deep understanding of Lean principles.
To identify the root causes of the performance issues, I conducted a value stream mapping exercise, visualizing the end-to-end customer service process and pinpointing bottlenecks and areas of waste. This analysis revealed inefficiencies in communication, redundant tasks, and delays in issue resolution.
I then facilitated a Kaizen event, bringing together a cross-functional team of customer service representatives, supervisors, and other stakeholders. We brainstormed solutions, prioritizing those that aligned with the Lean principles of delivering customer value and minimizing waste.
I implemented several Lean tools and techniques, including:
5S methodology: Organizing the workspace for efficiency and standardizing procedures.
Kanban boards: Visualizing the workflow and identifying bottlenecks.
Poka-yoke: Implementing error-proofing measures to prevent defects.
Root cause analysis: Using the "5 Whys" technique to uncover the underlying causes of problems.
Through continuous improvement and data-driven decision-making, we achieved significant results within six months:
Reduced customer complaint resolution time by 25%.
Improved customer satisfaction scores by 15%.
Increased employee engagement and morale.
Achieved full compliance with client service level agreements (SLAs).
This project demonstrated my expertise in applying Lean principles to transform operational processes, eliminate waste, and deliver measurable results. I am adept at leading cross-functional teams, facilitating collaboration, and driving continuous improvement initiatives.
Key Lean Tools and Methodologies: Value Stream Mapping, Kaizen, 5S, Kanban, Poka-yoke, Root Cause Analysis, Continuous Improvement (PDCA cycle)
© 2025. All rights reserved.
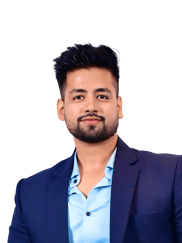
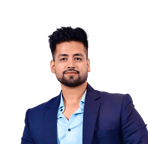